Contributed by: Mr Arpan Garg
Working underground is never easy, no matter what people may say. Have you ever feared while going inside the tunnel? Does it ever cross your mind that what will happen if it collapses, will I be able to survive and see the light of the day? Well, let me tell you, all these thoughts crosses in the mind of tunnel engineers/workers who are working in tunnel construction. Today, I am going to share my experience on tunnel construction in weathered rock. The construction process in weathered rock is not as easy as it seems from its name, rather it is one of the toughest while continuing through a weathered rock. As it is widely known, that a tunnel is an artificial/manmade underground passage, especially one built through a hill or under a building, road or river. Tunnels are not only structures constructed of concrete, steel, masonry and timber or bored into a rock but also for other numerous functional systems to perform various roles. Although, there are abundant methods defined for carrying out the underground construction but whenever a difficult situation arises like formation of cavities, flowing ground conditions, extremely fractured & weathered rock conditions, rock bursting etc. then only it is realized that to cater such anomalies the team requires courage, patience, experience and presence of mind in this time of crises to progress and achieve the progress with utmost safety.
Construction of Tunnel (Adit) in poor rock strata
The construction was started in March’2010 with conventional drilling and blast methodology. The rock encountered while constructing the portal of the Adit (having dia. 7.5 m, D-shaped) was Amphibolite which is a hard and competent rock. So it was a relief for the team that the expected rock will be the same throughout the tunnel, but there goes a saying “What’s the thrill of going easy in life” and soon the day arrived when the rock changed its behaviour and the whole optimism of the team was shattered. We hardly progressed around 25 m from the portal and there was loose fall from the face to which it was decided that more permanent supports like steel ribs (ISHB- 150×50) needs to be installed.
The Battle begins….
- Ribs and Fore-poling: – Ribs were installed and to pack the face, fore-poles having 25 mm dia. were installed, but due to the presence of 1 to 1.5 m thick phyllite rock band in the crown portion, the crown portion was mutilated and the small rock fragments fell down which was very disheartening after all the hard work put by the people in packing the face, but no hope was lost by the team, the rectification was completed and the portion behind the rib was backfilled by concrete.
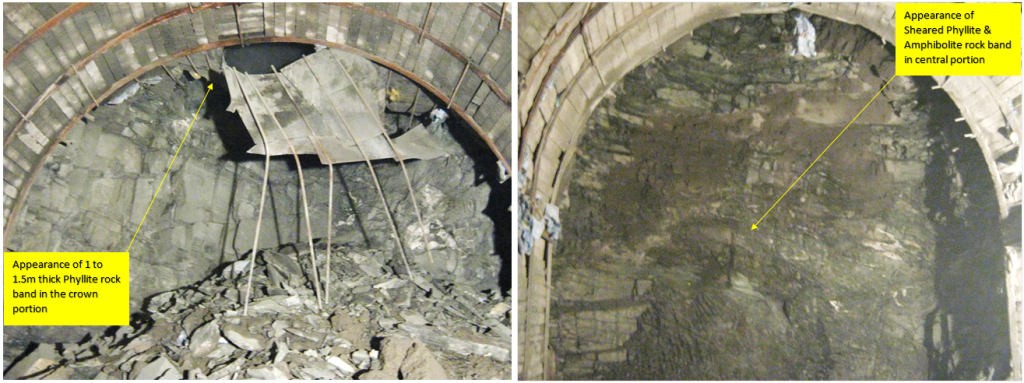
Progressing at snail pace: – Poor rock strata continued, as a result the progress started coming at snail pace. As we progressed inside, the deterioration of rock continued, and now various excavation methods were employed. Installation of ribs, lagging and backfill took more time resulting in more unsafe working condition due to less stand-up time of rock, so it was change to lattice grider, wiremesh and thick layer of sealing shotcrete. This pattern gave some additional safety benefits as well as strength benefits as the lower grade backfill was replaced by higher grade shotcrete and the amount of time during which workers remain in direct contact with the rock was also reduced.
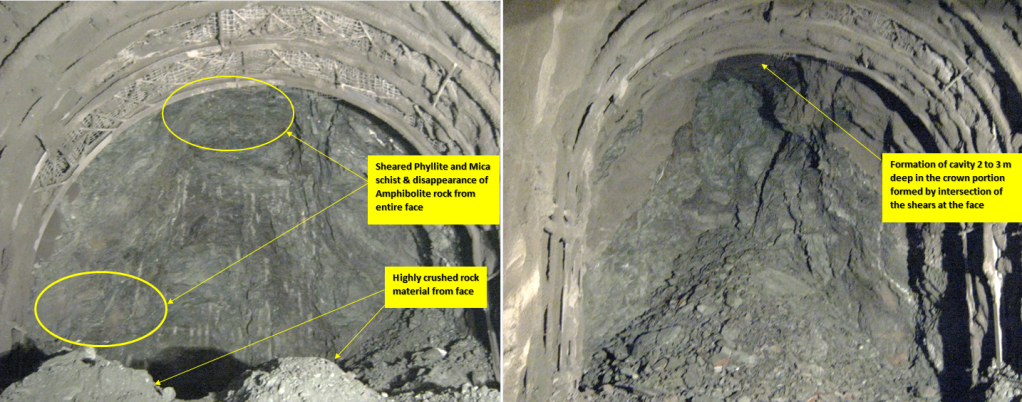
Cavity formation and treatment: – By this time, we got much versed with the geology of the rock and the various methods that can be employed to overcome if such situation arises. Again, the history repeated itself and we came back from where we started. Ribs, lagging, backfill came into the picture again but this time we did a slight improvisation by using another support system. This time Pipe roofing (Umbrella formation) was introduced to cover the cavity and to proceed further upto certain depth of the tunnel with comfort.
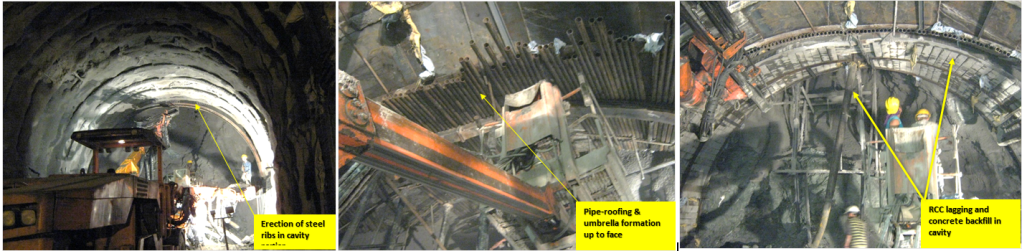
Excavation using twin cutter: – While the rock was very loose and falls under the category of sheared Micaceous Phyllite, it was the time when we first introduced a new digging machine called as Twin cutter which was also the first type of equipment to be used at our site in the project. It was a kind of machine which scratches the tunnel face due to lose nature of the rock and there was no need to take any blast or even no breaker was required which will disturb the surrounding area due to its vibrations. Twin cutter is basically an attachment that can be surmounted on an excavator with a cuter head having blades as can be seen in the picture below:
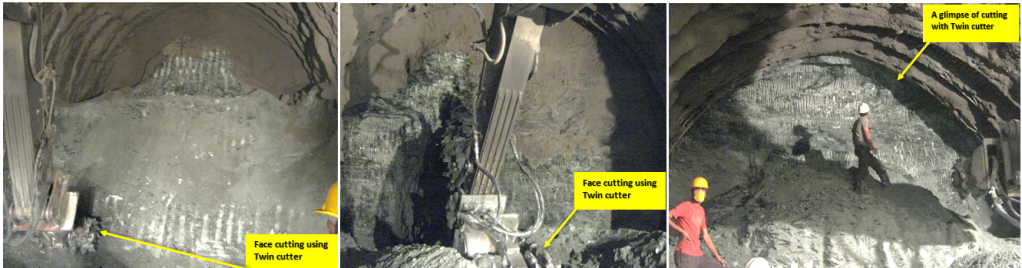
Elephants foot: – Although, twin cutter was deployed but still it was feared that due to excessive stress in the rocks and with very less stand-up time of the rock, it can collapse any time an there can be a chaos while proceeding inside. So, to overcome this possibility, only side cutting of the face was done i.e. space creation only for ribs/lattice girder erection and leaving the centre portion of the tunnel face as it is as shown in the fig. below. This kind of excavation was called as Elephant’s foot where the tunnel face is supported at the centre using its own weight. This method can be related to the Hindu epic Ramayana to as Angad’s foot where many potential people tried but none was successful in lifting his foot. This helped us in preventing the collapse of tunnel face by using its own weight as its support.
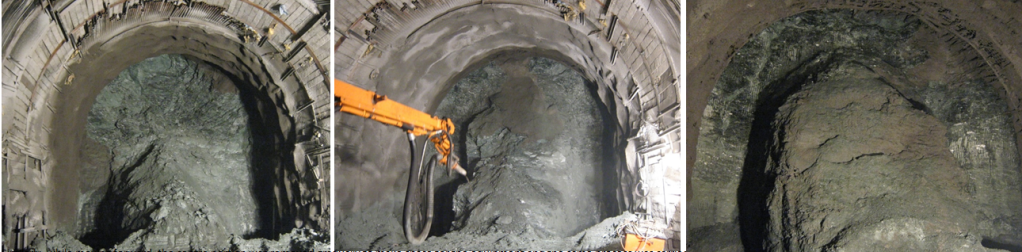
Similarly, while moving forward, the centre portion was removed gradually to make space for the equipment and the same process was carried on excavating the tunnel.
To conclude, I will only say that there can be plenty of methods which can be devised for safe tunnelling. It solemnly depends upon the in-depth knowledge, experience and the presence of mind which is needed while encountering these situations.
I hope you will find this helpful and can plan the excavation methodology accordingly.
Happy Tunnelling.
Happy to see TAIYM colleagues sharing experiences- something we have been missing in our industry. With social media platforms, it has become easy now and I appreciate this article. Perhaps more discussion can take place to analyse whether we could have done things differently so that we do not repeat the same mistakes and learn from experiences in our industry.
LikeLike